Kalkulacja TKW - z czego się składa i jak jest liczona w symulacjach produkcyjnych
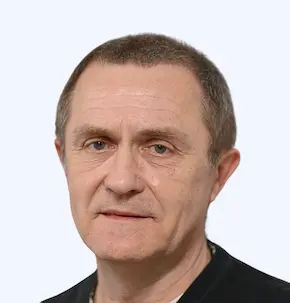
Techniczny Koszt Wytworzenia (TKW) to pojęcie stosowane oznaczające całkowity koszt wytworzenia określonego produktu lub usługi. Obejmuje on zarówno koszty bezpośrednio związane z procesem produkcyjnym jak i koszty pośrednie. TKW nie uwzględnia kosztów sprzedaży, marketingu czy administracji – skupia się wyłącznie na aspekcie produkcyjnym.
Koszty bezpośrednie produkcji
Są to koszty, które można jednoznacznie powiązać z produkcją określonych wyrobów gotowych.
- Bezpośrednie Koszty Materiałowe (BKM) – koszty surowców, materiałów i półproduktów, które są zużywane w procesie produkcyjnym. W przypadku rzeczywistych zleceń produkcyjnych będzie to koszt wynikający z wartości dokumentów RW i ich ewentualnych korekt.
- Bezpośredni Koszt Robocizny (BKR) – jest to koszt pracy bezpośrednio zaangażowanej w wytworzenie produktów. BKR jest liczony na podstawie czasów pracy ewidencjonowanych na podstawie zwrotnej informacji dostarczonej przez pracowników na „Karcie Pracy”. Tak wyliczony koszt pracy może być powiększony o stały współczynnik narzutu zawierający np. część ZUS-u płaconą przez pracodawcę.
- Koszt Maszynowy (KM) – koszt związany z wykorzystywaniem poszczególnych stanowisk produkcyjnych, zwany też czasami kosztem stanowiskowym. Uwzględnia między innymi zużycie energii i innych mediów, czas pracy maszyn wynikający z raportowanego z „Kart Pracy” czasu pracy, koszty narzędzi oraz też związane z utrzymaniem hali, odpisami amortyzacyjnymi, kosztem leasingu i utrzymaniem w ruchu.
- Koszt Usług Obcych (UO) – koszt kooperacji zewnętrznej, przy czym pod pojęciem kooperacji rozumiemy wyprowadzenie części procesu produkcyjnego do kooperanta zewnętrznego zarówno w zakresie obróbki czy też montażu, ale również np. badań zewnętrznych.
Do bezpośrednich kosztów produkcji zalicza się także Specjalny Koszt Wytworzenia (koszty oprzyrządowania specjalnego wytwarzanego na potrzeby realizacji poszczególnych składników) oraz Koszty Badań i Rozwoju (koszt opracowania dokumentacji oraz koszty ponoszone na badania i rozwój produktów). Zazwyczaj nie są one uwzględniane w standardowej kalkulacji doliczeniowej, można je jednak wykorzystać przeprowadzając kalkulacje metodą rachunku składników pokrycia.
Koszty pośrednie produkcji
Koszty pośrednie to cztery kategorie, które doliczamy procentowo jako narzut do poprzedzających kosztów bezpośrednich.
I tak, po bezpośrednim koszcie materiałowym mamy pośredni koszt materiałowy, jako narzut procentowy do wartości bezpośredniego kosztu materiałowego – czyli wkładu materiałowego w wyrobie – policzony według współczynnika procentowego na wartość BKM, na koszty związane z magazynowaniem, transportem lub materiałami ponadnormatywnymi albo materiałami dodatkowymi niepodlegającymi ewidencji magazynowej, a zaliczanymi od razu w koszty.
Po bezpośrednim koszcie robocizny doliczamy pośredni koszt robocizny (nazywany też kosztami wydziałowymi) jako narzut procentowy na płace charakterystyczny dla poszczególnych MPK.
Dwie pozostałe kategorie kosztów pośrednich to pośredni koszt zarządu i pośredni koszt zbytu. Te z kolei stanowią narzut procentowy na koszt produkcji będący sumą bezpośredniego kosztu materiałowego, pośredniego kosztu materiałowego, bezpośredniego kosztu robocizny, pośredniego kosztu robocizny, kosztów maszynowych, kosztu usług obcych oraz ewentualnego kosztu badań i rozwoju oraz specjalnego kosztu wytworzenia.
Dwie ostatnie kategorie mogą być klasyfikowane również jako koszty bezpośrednie, gdy wiadomo, jaki był np. koszt opracowania w stosunku do dedykowanego niepowtarzalnego wyrobu i ile kosztowało dla niego oprzyrządowanie specjalne.
Obliczanie TKW w oparciu o dane z systemu ERP
Obliczenie technicznego kosztu wytworzenia umożliwia określenie, ile faktycznie kosztuje wytworzenie poszczególnych produktów, racjonalne ustalanie cen sprzedaży, analiza rentowności produkcji danego produktu i oparte o dane planowanie finansowe.
Biorąc pod uwagę na jak szerokiej grupie czynników bazowane są kalkulacje TKW, dają one także możliwość identyfikowania obszarów, w których można zastosować optymalizacje dążące do redukcji kosztów i zwiększenia rentowności.
Produkcja.NET zawiera rozbudowany model umożliwiający łatwe obliczanie technicznego kosztu wytworzenia w oparciu o dane technologii i informacje z systemu ERP. Informacje o rzeczywistej wartości surowca w powiązaniu z konkretną partią dostawy, aktualnych kosztach mediów, wartości pracy zaangażowanych pracowników są pobierane z dedykowanych do ich obsługi modułów, a następnie wykorzystywane nie tylko w samym wyliczeniu TKW, ale też bardziej rozbudowanych symulacjach wytwarzania.
Symulacje wytwarzania w systemie Produkcja.NET
Symulacja wytwarzania jest wirtualnym zleceniem produkcyjnym, przygotowywanym w oparciu o technologię, bez względu na źródło jej pochodzenia. Na przykład na podstawie technologii zdefiniowanej w rejestrze głównym dla produktów wymienionych w dokumentach handlowych lub technologii wzorcowej w oparciu o parametry tego wzorca dla kalkulacji wyrobów podobnych.
Ma na celu szybkie oszacowanie kosztów własnych wyrobu (TKW) i możliwości jego wyprodukowania, z uwzględnieniem potrzeb materiałowych, aktualnego zatrudnienia oraz skutków obłożenia stanowisk produkcyjnych rzeczywistym zleceniem.
Symulacje tworzone mogą być w dwóch trybach:
- aktywna – w analizie obłożenia stanowisk dla innych generowanych symulacji, wielkości wygenerowane przez tę symulację będą uwzględnione, dzięki czemu możliwe jest określenie wykonalności zlecenia z perspektywy dostępności maszyn i pracowników.
- nieaktywna – to symulacja nie powiązana z żadnym istniejącym zleceniem produkcyjnym i jest ignorowana w analizie innych symulacji; tworzona jest na potrzeby analizy kosztów, a nie bilansu obciążenia stanowisk.
Symulacje można dowolnie tworzyć i usuwać, a także uruchamiać na ich podstawie zlecenia produkcyjne. Ponadto dla stworzonej wcześniej kalkulacji system daje możliwość ponownego jej przeliczenia: według aktualnych stawek lub według aktualnej technologii.
Przekalkulowanie według jednego z tych dwóch scenariuszy pozwala chociażby na śledzenie realnego kosztu wytworzenia budowanego prototypu lub aktualizację oferty w sytuacji wzrostu kosztów np. energii elektrycznej.
Tworzenie symulacji z dokumentów ZZ i ZS
Wybierając tryb symulacji „Z zamówienia handlowego” przygotowujemy ją w oparciu o dokumenty ZZ i ZS wybrane z podpowiedzianej przez system listy, którą możemy filtrować według kilku parametrów.
Symulacje można wykonywać dla całego dokumentu handlowego lub jego wybranych pozycji – umożliwia to narzędzie podglądu dokumentu. Za pomocą opcji „Pobierz do kalkulacji tylko niezrealizowane pozycje” pobierzemy do symulacji te pozycje, które nie zostały zrealizowane, czyli sprzedane.
Uruchomiona symulacja oddaje tabelę kosztów w formie kalkulacji doliczeniowej uwzględniającą wszystkie analizowane pozycje.
Przedstawiona w tabeli drzewiasta struktura złożenia produktów będących przedmiotem symulacji pozwala na poznanie ich kosztów na dowolnym poziomie złożenia. W zależności od tego, jaka część (lub cała symulacja) zostanie wskazana w drzewie struktury, wartości z poszczególnych pól będą odpowiadały tylko tej części.
Symulacja produkcji na podstawie ręcznie wybranej technologii
Ten typ symulacji obejmuje ręcznie stworzoną listę produktów wybranych z dostępnych technologii oraz ich zadeklarowane do obliczeń ilości.
Po wybraniu składnika/składników symulacji akcja uruchamiana jest dokładnie tak samo jak w przypadku symulacji z dokumentów handlowych, skutkując takim samym zakresem informacji.
Dodatkowe możliwości analizy kosztów produkcji
Dla niektórych pozycji kosztowych kalkulacji dostępne są dodatkowe informacje, pozwalające na szczegółową analizę w danym zakresie.
Bezpośredni Koszt Materiałowy (BKM) – koszt wkładu materiałowego liczony według sposobu wyceny określonego w konfiguracji parametrów symulacji. Zawartość okna szczegółów stanowi skomasowaną listę materiałów dla zaznaczonych pozycji lub całej symulacji.
Z tego poziomu można uzyskać informacje o zapotrzebowaniu, stanie dostępnym, aktywnych rezerwacjach oraz informacje na jakim magazynie znajdują się poszczególne materiały/towary.
W przypadku wyznaczania ceny według dostaw, system daje możliwość podglądu na podstawie jakich dokumentów została wyliczona cena jednostkowa wybranego surowca.
Zapotrzebowanie materiałowe, bez względu na to, jakiego węzła drzewa symulacji dotyczy, zawsze zawiera informację o potrzebach materiałowych przeliczonych dla podstawowej magazynowej jednostki miary oraz w tak zwanej technologicznej jednostce miary, czyli w jednostce, według której została wyliczona norma zużycia. Wyliczone potrzeby materiałowe są wielkościami rzeczywiście potrzebnymi, dla zrealizowania przeprowadzanej symulacji.
Oprócz ilości materiałów w tabeli ujęto także przypadające na każdy materiał bezpośrednie i pośrednie koszty materiałowe.
Bezpośredni Koszt Robocizny (BKR) – koszt płac z narzutami związany z wykonaniem prac przewidzianych Kartami Technologicznymi wyliczony zgodnie ze wskazanymi w operacjach kategoriami zaszeregowania.
Zestawienie przedstawia zapotrzebowanie na „pracę”, podzieloną na poszczególne grupy zawodowe, według słownika zawodów predefiniowanego w systemowym obszarze Administracja. Może ono być prezentowane według grup zawodowych uczestniczących w wykonaniu zlecenia (dla całej symulacji lub wskazanego węzła) z podaniem bezpośredniego i pośredniego kosztu robocizny oraz całkowitego czasu pracy (planowanego, czyli przy założeniu wyrobienia w wysokości 100% normy).
Drugą formą prezentacji jest zestawienie według MPK – prezentuje w tabeli wszystkie wydziały (gniazda) zaangażowane w symulowaną produkcję z podaniem bezpośrednich i pośrednich kosztów robocizny oraz całkowitego czasu pracy.
Koszt Maszynowy (KM) – koszty stanowisk produkcyjnych oraz ich obłożenie realizacją symulacji. Prezentowane w tym zestawieniu dane mogą być dodatkowo doprecyzowane przez horyzont planistyczny oraz uwzględnienie czynnych zleceń i innych aktywnych symulacji.
W tabeli wyświetlane są wszystkie stanowiska (o unikalnym kodzie), bez względu na ich zaangażowanie w proces produkcyjny.
Alternatywnie informacja o obłożeniu stanowisk może być prezentowana w dniach zajętości. W takim przypadku dla stanowiska o najdłuższej zajętości pasek wykorzystania wypełnia pole całkowicie, a w miejsce procentu wykorzystania wpisane są dni zajętości.
Koszty Usług Obcych – zestawienie kosztów wynikających z usług obcych np. kooperacji – wydzielenia części procesu produkcyjnego na zewnątrz. Uwzględnia informacje o materiale, kooperancie zewnętrznym oraz wartościach dla danych pozycji.